An Inductosyn is type of inductive position sensing device from Farrand Controls/ Ruhle Companies. Inductosyns work using the same basic physics as a transformer using planner arrays of inductive windings.
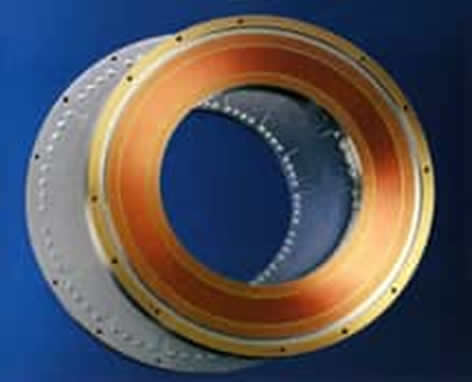
Product features of Inductosyn:
- Non-contact, inductive principles
- Comprises of a flat, disc shaped rotor & stator
- Energized and controlled by an external set of electronics
- Capable of extremely high accuracies, 1 arcsec (0.25 mdeg)
- Available in a wide variety of sizes
Good resistance to changes in temperature, environmental conditions (dust, etc).
Inductosyn versus new generation rotary encoders
In the past decade significant advances have been made in the performance of rotary encoders. Resolutions and accuracies which were previously only possible with an Inducotsyn or with an optical encoder in a controlled environment can now be achieved by off-the-shelf rotary encoders with the added convenience of on-board digital outputs such as SSI and BiSS. Furthermore, these modern rotary encoders are available at a fraction of the cost of the Inductosyn system and without ITAR restriction or export licenses. Additional benefits include the use of a passive rotor that requires no wiring and excellent resistance to shock and vibration due to lower mass.
A comparison of modern inductive, capacitive and the Inductosyn is shown below:
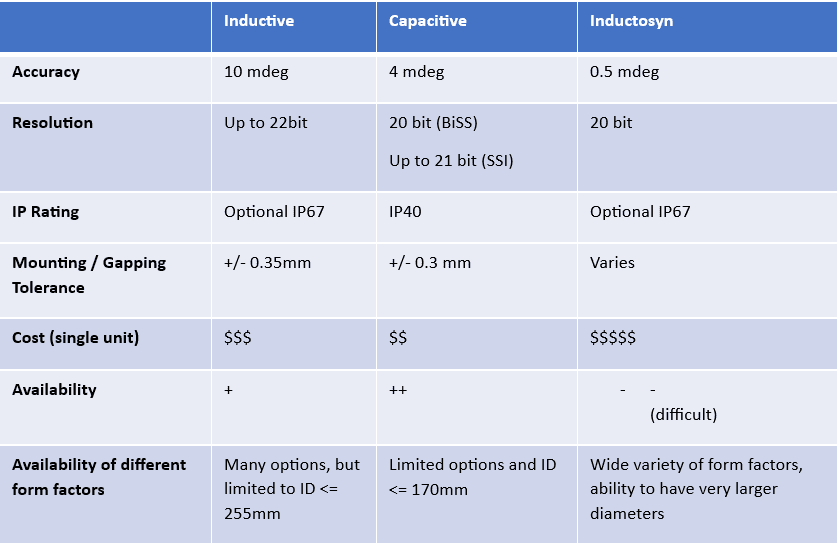
At Everight Position we take the time to learn about your application and can provide a path forward to maintain an existing Inductosyn setup as well as the potential migration to a modern rotary encoder. As a US corporation and NIST800.171 compliant, Everight Position can help each step of the way. We look forward to working with you.
"*" indicates required fields