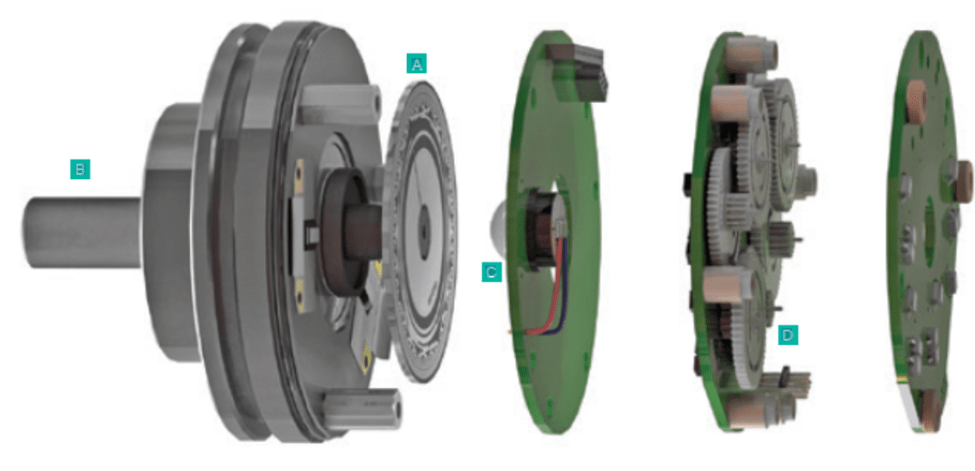
While the options may seem endless, with a little help specifying an encoder doesn’t have to be so daunting of a task. By starting with mechanics and working to electronics and communication protocol we can find work our way through a sea of options.
- Technology: Optical, magnetic, inductive or capacitive: If high accuracy is needed an optical or capacitive may be best, for a low-cost solution one may want to consider magnetic.
- Flange: How will you couple the encoder to the rotating axis.
- Traditional shaft (as shown above)
- Blind-hollow: Commonly called ‘hub-shaft’ , these encoders can be mounted directly on the end of the shaft, eliminating the need for a coupling.
- Through-hole: The shaft passes through the encoder. In ‘kit encoder’ configurations the rotor mounts directly to the shaft and the stator portion of the encoder is mounted to the adjacent chassis, eliminating the need for bearings, but requiring the user to maintain gapping tolerances.
- Communication Protocol: How will the encoder communicate the position data? Common protocols include traditional quadrature (incremental/ABZ) and analog (sin/cos) outputs as well as digital outputs such as SSI, BiSS-C, CANopen and Ethernet based protocols including EtherNet/IP, PROFINET, EtherCAT, MODBUS and others.
- Single Turn or Mulit Turn: A single turn encoder can report the angle 0-360 degrees but lacks the ability to differentiate between its position after multiple turns. A multiturn encoder uses gearing or batteries or energy harvesting such as Weigand Technology, to keep track of the number of turns.
- Environmental: Any extreme environmental factors to consider? High or low temperatures, shock, vibration, exposure to water, submersion.
At Everight Position we work the best rotary encoder manufacturers in the world, providing a broad range of options that is unrivalled by any distributor or OEM. Furthermore, several of our partners specialize in custom encoder projects for small and large customers alike, providing a truly endless range of options. To learn more take a look at our product finder (insert link to rotary encoders product finder) or better yet, give us a call and in a few minutes one of our experts can learn more about your application and find the best sensor for you.
Do you have questions?
"*" indicates required fields