While they may be small, the role of rotary encoders in spacecraft is vital, demanding a balance between performance, reliability, and the unforgiving environment of space. From NASA’s Robonaut II to automated material handling systems on the International Space Station, Everight has worked with engineers to put rotary encoders into ‘the final frontier.’
LEO (Low Earth Orbit): A Balancing Act
Low Earth Orbit (LEO) satellites, buzzing just a few hundred kilometers above Earth, are vital for tasks like communication, navigation, and Earth observation. Here, encoders play a crucial role in antenna pointing mechanisms. LEO satellites need to constantly adjust their antennas with incredible precision to maintain communication with ground stations. Rotary encoders provide the high resolution feedback loop for these adjustments, ensuring optimal signal strength and uninterrupted data transmission. The compact size and low power consumption of certain encoder models are well-suited for the weight and energy constraints of LEO spacecraft. Some LEO constellations may even house hundreds or thousands of satellites, making cost-effective and reliable encoders even more critical. For example, SpaceX’s Starlink satellite internet constellation has on the order of 6,000 satellites in LEO.
GEO (Geostationary Orbit): Stable and Precise
Geostationary Orbit (GEO) satellites, hovering at a much higher altitude of 36,000 kilometers, maintain a fixed position relative to Earth’s surface. This makes them ideal for applications like weather monitoring and satellite television broadcasting. In GEO, encoder requirements become even more stringent. Unlike LEO, GEO satellites are constantly bathed in the harsh radiation of the sun. Here, robust materials and specialized shielding become essential to protect the encoders from degradation and ensure they function flawlessly for their designed lifespan, often exceeding 15 years. Operation under vacuum pressure and appropriate outgassing also becomes important. Additionally, the need for long-term, uninterrupted operation demands high reliability and redundancy. In case of a primary encoder failure, a backup encoder can take over seamlessly, preventing catastrophic mission loss.
Deep Space: Venturing into the Unknown
Venturing beyond Earth’s orbit, deep space exploration throws unique challenges at encoders. Here, the focus shifts towards fault tolerance and extreme durability. Deep space probes and rovers encounter vast distances, harsh radiation environments, and extreme temperature variations. Unlike missions closer to Earth, communication times can stretch to hours or even days, making remote troubleshooting difficult. Encoders designed for these missions are often custom-built to withstand such conditions, ensuring crucial maneuvers and data collection can be performed flawlessly, even in the event of a single-point failure. Some encoders may incorporate redundancy within themselves.
The Rise of Commercial Space and the Future of Encoders
With the commercial space industry booming, the demand for reliable and cost-effective commercial-off-the-shelf (COTS) encoders is on the rise. Built upon MIL, EEE and ESA standards, manufacturers are developing new encoder models that are lighter, more energy-efficient, and commercially priced, making them suitable for a wider range of space applications, from constellations of small LEO satellites to deep space probes venturing beyond our solar system. One example is the Netzer VLS-60 which has Parylene conformal coating and a design built to withstand 30kRad. Additional VLS encoders are available up to 170mm outer diameter. The increasing emphasis on commercial space endeavors will likely drive further innovation in encoder technology, making them even more miniaturized, radiation-resistant, and adaptable to the ever-changing needs of space exploration.
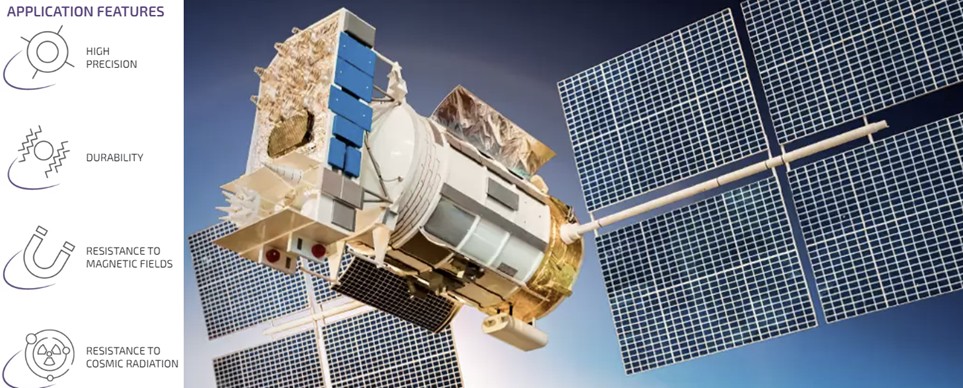