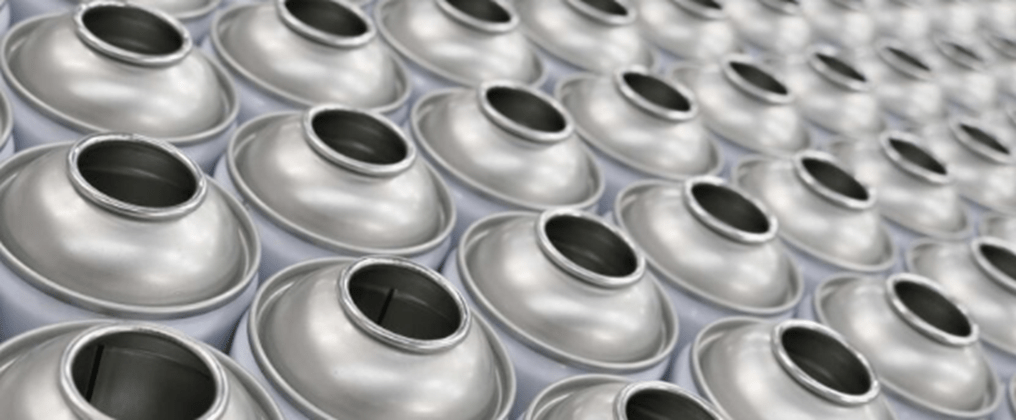
Enhancing Safety and Efficiency in Hazardous Environments
Introduction
In the competitive world of aerosol and bag-on-valve filling, ensuring both efficiency and safety on the production line is paramount. This case study explores how one leading company in the industry leveraged cutting-edge technology to meet these dual objectives. By integrating Positek linear sensors into their filling line, the company achieved significant improvements in operational safety and reliability.
Background
The company, established in the early 2000s, specializes in the production of various aerosol products and bag-on-valve systems. These products are widely used in industries ranging from personal care to pharmaceuticals. Given the nature of their operations, the company faces numerous challenges, including the need to maintain high precision in filling processes and to operate in potentially hazardous environments due to the volatile nature of the substances handled.
Challenges
One of the primary challenges faced by the company was ensuring that their filling lines could operate safely and efficiently in environments where flammable gases and liquids are present. Traditional industrial sensors were prone to corrosion and lacked the necessary certification for use in hazardous areas, leading to safety concerns. Finding an appropriate solution was critical to grow the business, as common household goods such as hair spray, alcohol, paint, flour and many aerosol propellants are flammable.
Solution: Positek Linear Sensors
After an extensive evaluation of available technologies in 2011 the company decided to adopt Positek X101 series linear sensors for their filling lines. Positek sensors are known for their reliability, precision, and suitability for use in challenging conditions.
ATEX Rating for Hazardous Environments
A key factor in the decision was the ATEX rating of Positek X series linear sensors. This certification indicates that the sensors are safe to use in explosive atmospheres, a critical requirement for the company’s operations. The ATEX rating ensured that the sensors could withstand and operate safely in environments with high levels of flammable gases and liquids, significantly reducing the risk of accidents and enhancing overall safety. X series sensor achieve this rating by being coupled with an intrinsically safe barrier, the X005.
Positek X101 series are available in stroke lengths from 2mm to 1000mm and feature a variety of different mechanical mounting options for easy integration into new and existing machiery
Stainless Steel Construction
Another significant advantage of Positek linear sensors is their stainless steel construction. This material choice offers exceptional durability and resistance to corrosion, making the sensors ideal for use in the company’s filling lines where they are exposed to various chemicals and environmental conditions. The rugged construction of the sensors ensures a longer lifespan and reduces the need for frequent replacements, contributing to lower maintenance costs and increased operational uptime.
Conclusion
The adoption of Positek linear sensors has proven to be a game-changer for the aerosol and bag-on-valve filling company. By addressing the critical challenges of operating in hazardous environments and ensuring the durability of their equipment, the company has set new standards for safety and efficiency, protecting employees and consumers alike. This case study highlights the importance of selecting the right technology to overcome operational challenges and achieve long-term success.