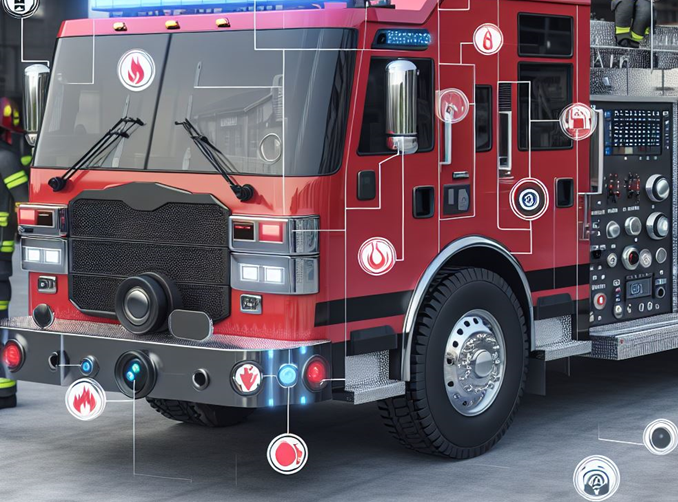
Enhancing Precision and Reliability
Introduction
Modern fire trucks are equipped with advanced technologies to ensure they operate efficiently and safely. As each truck is built to order, sensor technologies need to be flexible and easily integrated. This application note explores the use of rotary encoders in fire trucks, focusing on their implementation in fluid swivels for ladders, steering systems in tiller trucks, and linear positioning of outriggers.
Fluid Swivels for Ladders
Functionality and Importance
Rotary encoders are crucial in fluid swivels and sliprings for swivels on fire trucks. Common on ladders and other equipment, these require precise control and positioning to ensure the safety and effectiveness of firefighting operations. Fluid swivels facilitate the reliable passing of large volumes of water to hoses on the ladder, while ensuring the safe and accurate positioning of the ladder itself. Sliprings are used to pass electronic signal and power.
Steering Systems in Tiller Trucks
Rotary encoders are integrated into the tiller’s steering mechanism to provide precise feedback on the angular position of the rear wheels. This information is critical for the tillerman to make accurate steering adjustments, ensuring the truck’s stability and maneuverability.
Linear Positioning of Outriggers
Application of Rotary Encoders
Rotary encoders are often combined with a ‘draw wire’ to monitor the linear positioning of outriggers. These devices measure the extension and retraction of the outriggers, providing precise data on their position. The control system uses this information to deploy the outriggers to the correct length and height, ensuring optimal stability. Combined with an inclinometer to provide leveling information, the leveling process can be largely automated.
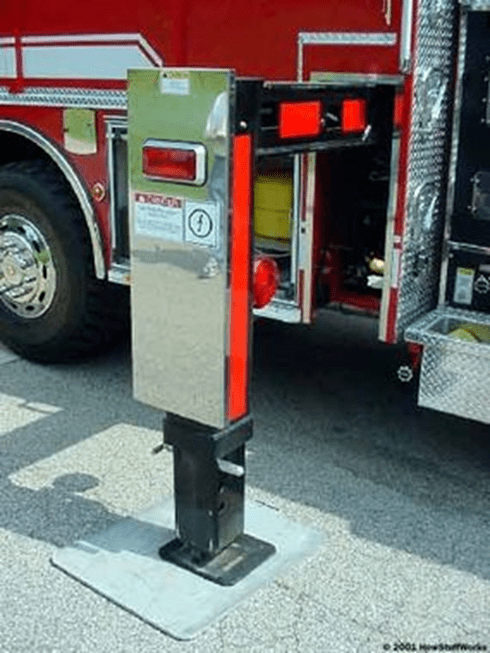
Easy to Integrate, Easy to Maintain
Most modern firetrucks rely on SAEJ1939 communication. At Everight we offer a variety of rotary encoders that support this protocol, making for easy and cost-effective integration. These encoders are battery-free, gear-free absolute sensors, meaning that they know their position immediately at start-up and do not have to be re-homed following a loss of power. This is especially helpful as a firetruck may not be powered for safety reasons while undergoing maintenance for example. By not relying on a battery backup, the regular step of battery replacement and the risks of battery malfunction are eliminated.
Other options include a wide variety of mechanical options, from low-cost end-of-shaft designs to large through-hole. IP68/69K environmental ratings ensure longterm reliability despite regular exposure to pressurized water hoses, variable temperatures and vibrations.
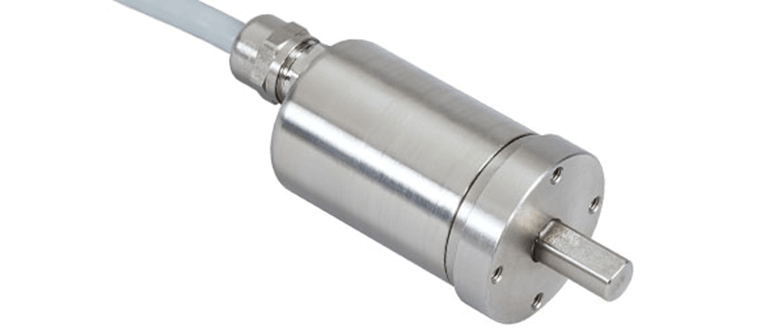
Future Prospects
As processes on firetrucks become automated, sensors such as rotary encoders will become more critical. Redundant encoder options can already provide independent, two channel position information in axes where positioning is most critical.