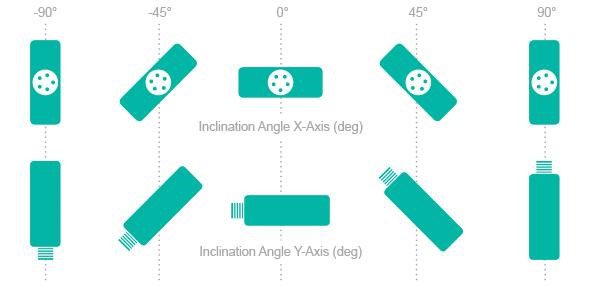
For applications where sudden movements, shocks, and vibrations are likely to be encountered, it is important to have sensors with fast response and a clean signal output. POSITAL’s dynamic inclinometers combine two measurement principles using two different MEMS sensors: a 3D acceleration sensor and a 3D gyroscope. The 3D acceleration sensor is not damped (unlike the units used in static inclinometers) and can follow rapid dynamic motions. At the same time, the 3D gyroscope measures rotational speeds, based on inertia principles. Signals from the accelerometers and gyroscopes are combined to produce an inclination measurement that fully compensates for the effects of accelerations. As a result, dynamic TILTIX inclinometers can be used reliably on mobile equipment such as construction machinery, mining equipment, cranes, or robotic applications.
The diagram below compares the performance of a dynamic inclinometer with an integrated gyroscope with the output from a conventional static inclinometer when both instruments are subjected to dynamic movements that involve heavy shocks and vibrations.
Tilt Measurement on a Moving Excavator
Innovative Algorithm for Reliable Results
The accelerometer measures the tilt position, while the gyroscope determines the rate of rotation. Accelerations have a huge impact on the accelerometer, but a limited effect on the measured rotation rates of the gyroscope. An innovative algorithm combines both signals, to get the best value out of each sensor. This way the sensor is able to separate the actual position value from the errors introduced by external accelerations.
Range and Mounting Option
The TILTIX series of inclinometers is available in two variants.
1. A dual axis sensor that is used for horizontal mounting. This version got two outputs, one for the X-Axis and one for the Y-Axis. Each of the axes shows the tilt angle with respect to the field of gravity.
2. A single axis tilt measurement version intended for vertical mounting with one axis output.
Additional Functionalities of the Dynamic Inclinometer
The main purpose of dynamic inclinometers is to provide stabilized data for tilt angles without the need for configuring any sensor parameters. However, for the dynamic inclinometer with CANopen interface, it is also possible to output the acceleration forces (accelerometer) and rotation speed (gyroscope) separately for each of the three axes. These measurements are stored in mappable CANopen objects.
Monitoring the acceleration force along one or more axes can be used, to implement additional functions or safety features on the controller side. The controller could stop the machine when a certain acceleration threshold is exceeded. With the additional information about the rotation speed in the x-axis, it is possible to measure and monitor the horizontal (yaw-) rotation of the machine. It is up to the machine builder or system integrator to decide how this additional information might be used.
Data Processing
A high-performance microcontroller is used to evaluate the sensor signals in real-time and calculate the corrected slope angle. Temperatures are also measured and used by the compensation algorithms to correct for unwanted effects. Intelligent digital filter algorithms reduce ambient noise and vibration to provide a precise and stable signal under all environmental conditions.
Non-linearities in the MEMS sensors are identified through a series of reference measurements made during the production process. These non-linearities are stored as a set of calibration data within the sensor. During operation, the calibration data are used to correct the MEMS sensor raw values and output an accurate linearized tilt angle. Customized parameters like an offset correction (Preset) and a scaling function (in case of analog output signals) can be added by the customer.
Manufacturing of MEMS Sensor Chips
Due to the advances in the manufacturing of Micro-Electro-Mechanical Systems (MEMS) devices, these kinds of sensors have become mass-market products with an excellent performance/cost ratio. The basic measuring component in TILTIXinclinometers is a MEMS sensor cell that is embedded in a fully encapsulated ASIC.
Common Specs
Sensor cycle time: This is the internal cycle time of the base sensor. A cycle time of 5ms means that the position value is updated every 5ms.
Interface cycle time: This is the cycle time the position value is transmitted via the communication interface. In contrast to the sensor cycle time (which is a fixed value), the interface cycle time can be easily adjusted by the customer at the interface level.
Absolute accuracy: The absolute accuracy is the worst-case deviation between the measured position and the actual position within the defined range.
Offset: When the inclinometer is positioned at the zero level, the output will show a small deviation. This error at the zero level is referred to as offset error.
Dynamic accuracy: This accuracy is determined the same way as the absolute accuracy, only that the device is exposed to external vibrations and accelerations. The dynamic accuracy was determined during lab tests on different equipment that simulate the moving environment of mobile machines. The stated dynamic accuracy serves as reference value; we recommend evaluating the dynamic behavior on your own machine, as vibrations and shocks differ from machine to machine. Lab tests were done with the following equipment:
Linear accelerations: The sensor is accelerated in one axis with 10 m/s² over 1s
Vibrations: Different vibration frequencies between 1-1000 Hz with a force of 1g
Resolution: This is the smallest possible step
Hysteresis: The definition of a hysteresis is that the output value of a system is not only dependent from the actual input, but also from past inputs. For inclinometers, this means that the measured tilt angle is also dependent on the past position. There will be a small difference whether the inclinometer is tilted from 0° to 10° or from 20° to 10°. This difference is described by the hysteresis.
Temperature gradient: This value describes the change of the measured tilt angle for a change in temperature. If the inclinometer is in a static position and the temperature decreases or increases, the output value will also change according to the temperature gradient.
Settling time: This is a value that describes the dynamic behavior of a system. The settling time defines the time the inclinometer signal needs to reach and stay within 5% of the final position.
Think POSITAL’s dynamic inclinometers may be your perfect fit? Fill out the form below to discuss this solution further.
"*" indicates required fields