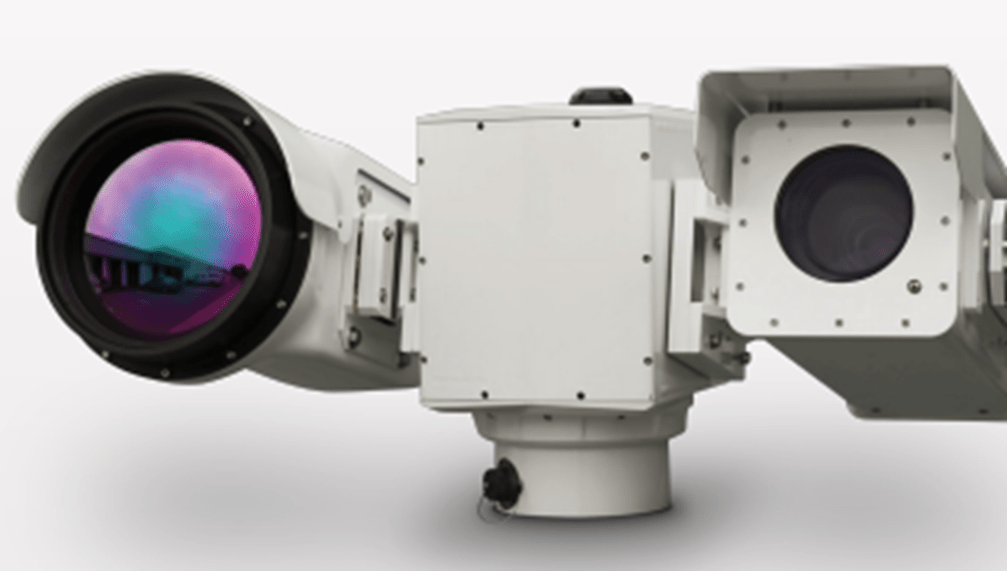
A Case Study on Electro-optical/infrared (EO/IR) Vision Systems
Introduction
In the realm of modern vision systems, precision and reliability are paramount. Used by defense, homeland security and municipalities alike, Electro-optical/infrared (EO/IR) systems rely heavily on accurate positioning mechanisms to ensure optimal performance. One critical component that plays a significant role in the azimuth and elevation (pan and tilt) positioning of these systems is the rotary encoder. This application note delves into the importance of rotary encoders, their functionality, and their impact on the performance of surveillance systems.
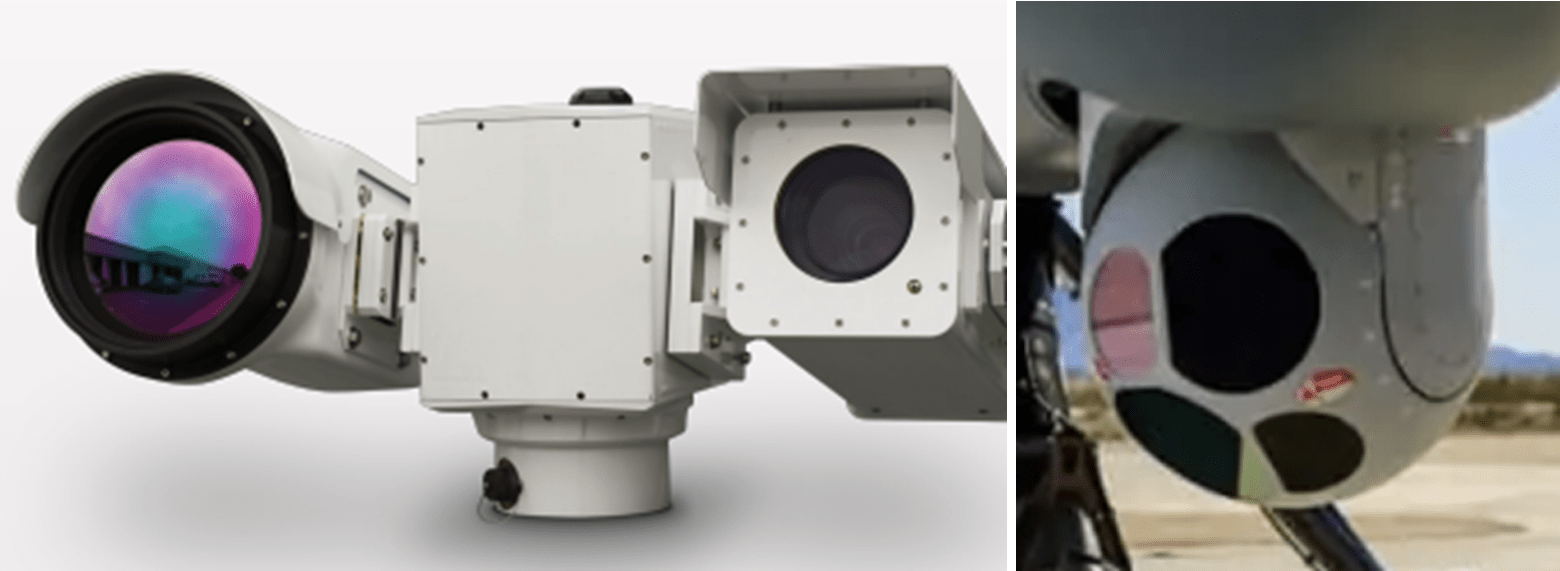
Understanding Rotary Encoders
Rotary encoders are essential for providing precise feedback on the position, speed, and direction of rotation. Rotary encoders come in various types, including optical, magnetic, capacitive and inductive, each with its unique advantages and applications.
Azimuth Positioning
Azimuth positioning refers to the horizontal rotation of the surveillance camera or sensor. It is essential for covering a wide field of view and tracking moving targets. Rotary encoders provide real-time feedback on the angular position of the azimuth motor, allowing the system to adjust the camera’s orientation with high precision. This ensures that the camera can swiftly and accurately follow a target, enhancing the overall effectiveness of the surveillance system.
Elevation Positioning
Elevation positioning, on the other hand, involves the vertical movement of the camera or sensor. It is crucial for adjusting the angle of view to cover different elevations, such as monitoring from ground level to higher altitudes. Rotary encoders provide precise feedback on the elevation motor’s position, enabling the system to make fine adjustments and maintain the desired angle. This is particularly important in applications such as perimeter security and aerial surveillance, where accurate elevation control is vital.
Implementation of Rotary Encoders
At Everight Position we have worked on a variety of projects, from one-offs to large volume OEM designs. While the overall objective may be similar, each application brings with it its own set of challenges and design criteria. Factors such as fixed vs mobile, temperature range, exposure to the outdoors and high altitudes, mechanical considerations and cost all play a role in determining the best encoder option.
In EO/IR systems, encoders provide continuous feedback on the position, ensuring that the camera can be accurately directed towards the target area, as this is critical in the initial focusing in such long-range vision system. The high-resolution feedback from the encoders allows for smooth and precise movements, minimizing the risk of overshooting or drifting. Signal latency of an encoder must also be considered, if too large the system will not be able to react fast enough to movement and will lose focus.
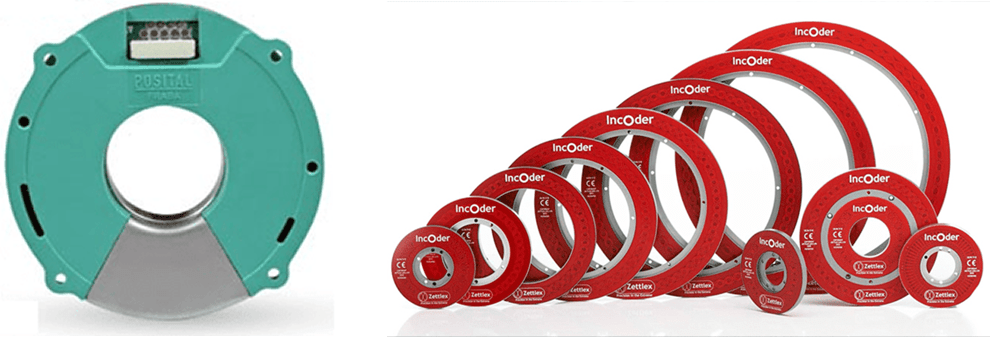
Benefits of Rotary Encoders in EO/IR
- Enhanced Accuracy: The precise feedback from rotary encoders ensures that the camera’s position can be accurately controlled to 2 millidegrees.
- Reliable Tracking: Holistic encoder designs provide more robustness to mechanical misalignment, shock, vibration and temperature shifts compared to single ‘point’ based technologies such as optical encoders. This is due their angle calculation being based on a measurement over the full 360 degree surface of the rotor
- Improved Responsiveness: The high-resolution feedback, up to 24 bits, from the encoders allows for fine adjustments to the camera’s position, enhancing the system’s responsiveness to moving objects.
Conclusion
Given the broad range of EO/IR camera systems it comes as little surprise that there is no ‘one-size-fits-all’ approach when it comes to rotary encoders. Each application brings with it its own requirements and challenges. At Everight Position we have worked with engineers for over a decade, step-by-step, helping to find the right encoder solution for each project.