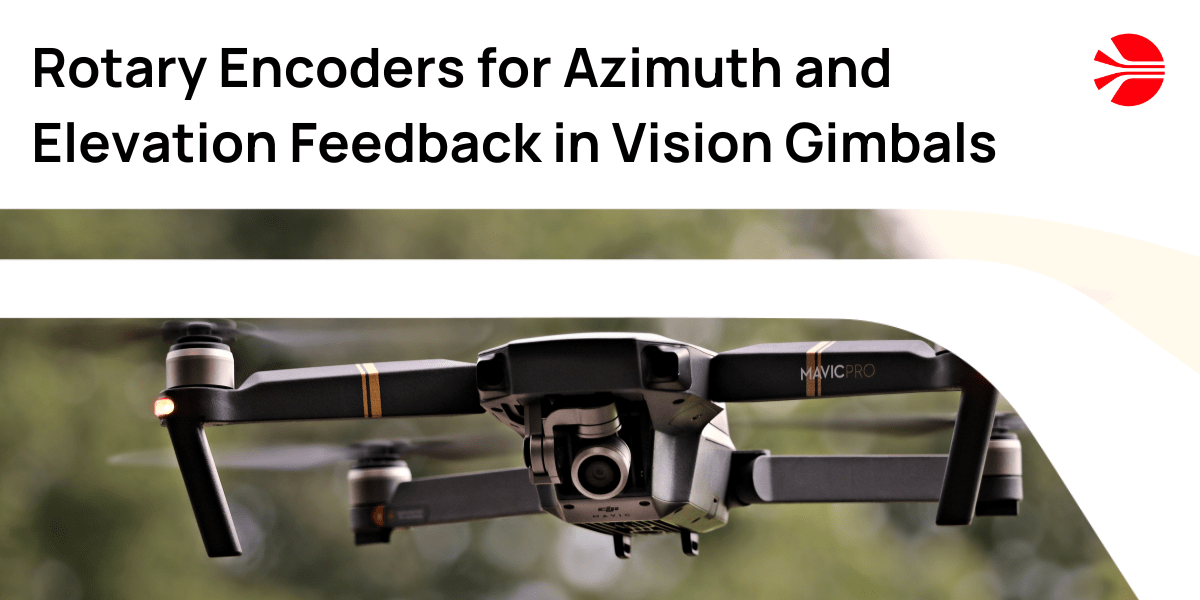
Introduction
Vision gimbals are critical components in various applications, including unmanned aerial vehicles (UAVs), robotics, and surveillance systems. Used in IR, LIDAR, visible light and other frequencies, they stabilize cameras or sensors, providing smooth and accurate footage or data acquisition regardless of platform movement. Rotary encoders play a vital role in achieving this stability by measuring the angular position of the gimbal axes, typically azimuth and elevation.
Azimuth and Elevation in Vision Gimbals
- Azimuth: Represents the horizontal rotation of the gimbal, rotating the camera left and right.
- Elevation: Represents the vertical rotation of the gimbal, tilting the camera up and down.
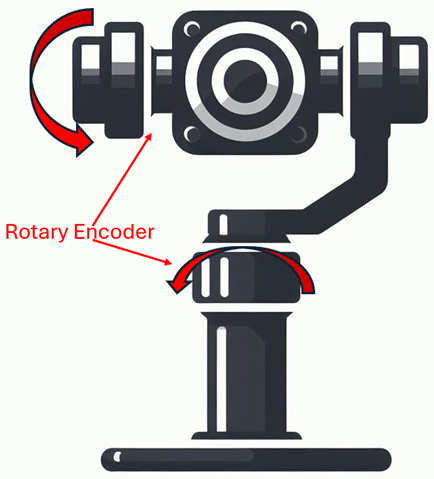
Accuracy vs Resolution
While sometimes accuracy, resolution and repeatability are used interchangeability in everyday vernacular, it is important to take a step back and define each as with respect to a gimbal system. In some applications high resolution is critical, allowing for a camera to remain ‘locked’ on a given object miles away. Small movements of the object may require extremely fine panning of the camera which comes as resolution, as too large of a step will cause the camera to move beyond the object.. Accuracy and repeatability can be more critical for initial startup. For more information on these important terms refer to the blog post Accuracy, Resolution and Repeatability here ( https://evrtp.com/?s=repeatability ).
Rotary Encoder Selection for Vision Gimbals
Other factors influence rotary encoder selection for vision gimbals:
- Speed: The encoder must respond quickly to rapid movements of the gimbal to maintain image stability.
- Latency: For applications where velocity and acceleration of the gimbal is needed significant fixed and variable latency can result in ‘noisy’ calculations and choppy movement.
- Size and Weight: For UAV and other weight-sensitive applications, compact and lightweight encoders are preferred.
- Power Consumption: Low-power encoders are ideal for battery-powered systems to extend operation time.
Common Rotary Encoder Types for Vision Gimbals
- Optical Encoders: Use light interruption or reflection to generate digital pulses representing angular position. They offer high resolution and accuracy, but can be sensitive to dust and vibration making longterm field use more difficult.
- Magnetic Encoders: Employ magnetic fields to generate position data. They are generally more resistant to dirt and vibration compared to optical encoders but with lower resolution and accuracy. Multiple redheads can improve performance, but results in higher costs and more complex computations.
- Inductive Encoders: Most practical for applications that require a large through-hole. High resolution and accuracy available, excellent robustness to environmental factors such as dust, dirt, water, etc.
- Capacitive Encoders: Ideal for compact locations, with diameters as small as 16mm. High accuracy and resolution at any size, but need to be protected from water and condensing humidity.
Integration of Rotary Encoders in Vision Gimbals
Rotary encoders are typically mounted on the gimbal axes, directly measuring the rotational movement. The encoder output, most commonly a digital output such as SSI or BiSS is then fed into the gimbal control system, which utilizes this data to:
- Drive the gimbal motors: The control system calculates the necessary motor commands to compensate for platform movements and maintain the desired camera orientation.
- Implement image stabilization algorithms: The encoder data can be used in conjunction with gyroscope and accelerometer data to further stabilize captured images or sensor readings.
Mobile Platforms: As camera systems become more advanced and automated, for example for arrays of cameras on automated tracks, the information on gimbal positioning becomes evermore important.
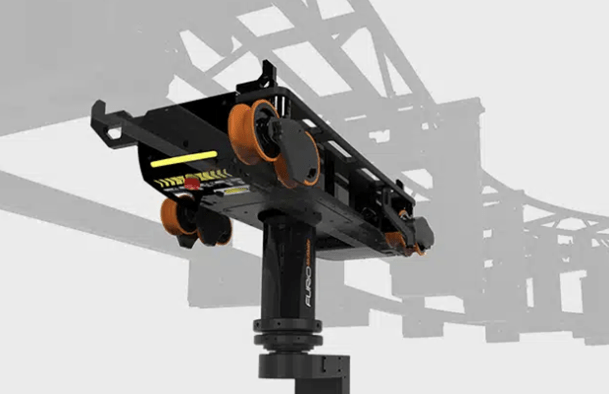
Conclusion
Rotary encoders are essential components for achieving precise and stable camera positioning in vision gimbals. Careful selection of encoders based on application-specific requirements ensures optimal performance and high-quality image or sensor data acquisition.Still have questions, that’s great, contact Everight Position and we can work together to find the best solution for your gimbal application.
Do you have questions?
"*" indicates required fields